
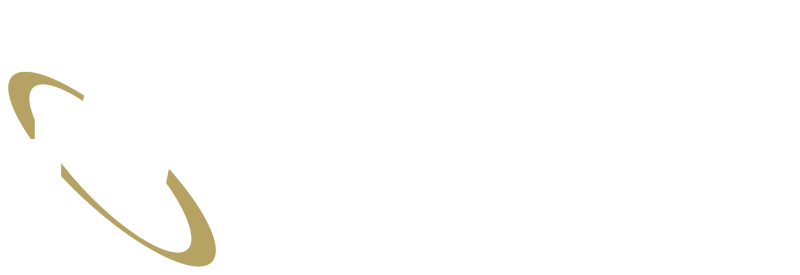
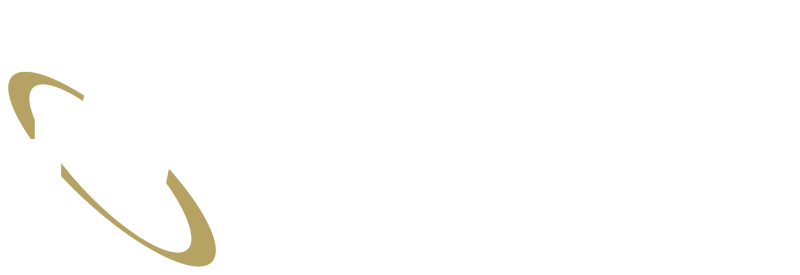
Il piano del governo italiano per l’Industria 4.0, contenuto all’interno della legge di Bilancio 2017, nasceva con l’obiettivo di mobilitare investimenti privati aggiuntivi in ricerca, sviluppo e innovazione con focus sulle tecnologie 4.0, proponendo un mix di incentivi fiscali con lo scopo ultimo di favorire e incentivare le imprese ad adeguarsi e aderire pienamente alla quarta rivoluzione industriale.
Durante la pandemia da Covid-19, le tecnologie ad essa collegate si sono rivelate fondamentali per contrastare la crisi. Tanto che nel 2021 il presidente del Consiglio, Mario Draghi, ha espresso la necessità di “estendere e rendere facilmente fruibile il piano nazionale della Transizione 4.0 per accompagnare le imprese nel processo di innovazione tecnologica e di sostenibilità ambientale”.
Anche per il 2023 le misure e gli incentivi hanno trovato conferma, evolvendosi e adattandosi al contesto economico e integrando negli obiettivi di transizione tecnologica anche quelli green. Vediamo come si evolve lo scenario di riferimento.
Cos’è l’industria 4.0?
L’industria 4.0 è un processo che scaturisce dalla quarta rivoluzione industriale e che sta portando alla produzione del tutto automatizzata e interconnessa. Finora le rivoluzioni industriali del mondo occidentale sono state tre:
- nel 1784 con la nascita della macchina a vapore per meccanizzare la produzione
- nel 1870 con il via alla produzione di massa attraverso motore a scoppio e petrolio come fonte energetica
- nel 1970 con la nascita dell’informatica, dalla quale è scaturita l’era digitale e l’automazione grazie a sistemi IT (Information Technology)
La data di inizio della quarta rivoluzione industriale non è ancora stabilita, probabilmente perché è tuttora in corso e solo a posteriori sarà possibile indicarne l’atto fondante.
Quali sono le sue aree di applicazione?
Le nuove tecnologie digitali hanno un impatto profondo nell’ambito di quattro direttrici di sviluppo.
- La prima riguarda l’utilizzo dei dati: la potenza di calcolo e la connettività si sostanzia in big data, open data, Internet of Things, machine-to-machine e cloud computing per la centralizzazione delle informazioni e la loro conservazione.
- La seconda è quella degli analytics: una volta raccolti i dati, bisogna ricavarne valore. Oggi solo l’1% dei dati raccolti viene utilizzato dalle imprese, che potrebbero invece ottenere vantaggi a partire dal “machine learning”, dalle macchine cioè che perfezionano la loro resa “imparando” dai dati via via raccolti e analizzati.
- La terza direttrice di sviluppo è l’interazione tra uomo e macchina, che coinvolge le interfacce “touch” e la realtà aumentata.
- Infine c’è la manifattura additiva, la stampa 3D, la robotica, le comunicazioni, le interazioni machine-to-machine e le nuove tecnologie per immagazzinare e utilizzare l’energia in modo mirato, razionalizzando i costi e ottimizzando le prestazioni.
Industry 4.0: quali sono i suoi impatti?
Dalla ricerca “The Future of the Jobs“, presentata al World Economic Forum 2016, è emerso che nei prossimi anni fattori tecnologici e demografici influenzeranno profondamente l’evoluzione del mercato del lavoro. Alcuni stanno influenzando le dinamiche già adesso e lo faranno ancora di più nei prossimi. L’effetto probabile potrebbe essere la creazione di 2 nuovi milioni di posti di lavoro, ma contemporaneamente ne spariranno 7, con un saldo netto negativo di oltre 5 milioni di posti di lavoro.
L’Italia ne potrebbe uscire con un pareggio (200mila posti creati e altrettanti persi), meglio di altri Paesi come Francia e Germania. A livello di gruppi professionali le perdite si concentreranno nelle aree amministrative e della produzione: rispettivamente 4,8 e 1,6 milioni di posti persi. Secondo la ricerca, compenseranno parzialmente queste perdite l’area finanziaria, il management, l’informatica e l’ingegneria.
Cambiano di conseguenza le competenze e abilità ricercate: il problem solving rimarrà la soft skill più ricercata, ma diventeranno più importanti il pensiero critico e la creatività.
Fabbrica 4.0: quali competenze richiede?
Le imprese stanno incontrando crescenti difficoltà per individuare, sia a livello di diplomati sia di laureati, le competenze necessarie per l’Industria 4.0. La scuola superiore e anche l’università non risultano ancora in grado di formare in modo adeguato le persone per garantire loro un inserimento efficace e rapido nel mondo del lavoro.
Servono competenze digitali, ovvero quel vasto insieme di abilità tecnologiche che consentono di individuare, valutare, utilizzare, condividere e creare contenuti grazie alle tecnologie informatiche e a Internet.
Come ci si forma all’Industria 4.0?
In realtà, prima di approdare in fabbrica o in azienda, i giovani non vengono preparati a sufficienzaall’Industria. Occorre perciò che la scuola faccia la sua parte. Per lo sviluppo delle competenze digitali potrebbero svolgere un ruolo chiave gli istituti tecnici e i licei che dovrebbero sviluppare orientamenti verso l’ottenimento di competenze certificate. Queste potrebbero consentire una effettiva employability dei giovani aprendo le porte al Lavoro 4.0.
Come si applicano le tecnologie 4.0?
Industria 4.0 non significa solo introdurre nuovi macchinari in azienda ma anche e soprattutto cambiare modello di organizzazione. La tesi che emerge da molte ricerche e dai dati Istat è la difficoltà (culturale) di due imprese su tre nell’adottare una architettura produttiva adeguata alla prospettiva dell’economia globalizzata.
Al netto di oggettive cause Paese (come la scarsità di investimenti pubblici, la lentezza della giustizia, o la fiscalità) e di incertezze caratteristiche (come quelle legate agli alti insuccessi dei passaggi generazionali o del difficile accesso al credito), il freno che gioca un ruolo formidabile è dato da alcuni stereotipi organizzativi.
Per esempio si pensa che l’organizzazione nelle Fabbriche 4.0 debba essere chiusa e gerarchica, e i manager ossessionati dal taglio dei costi. Invece, occorre puntare alla “via alta” dell’innovazione.
a cura di Theorema (info@theorema.eu)